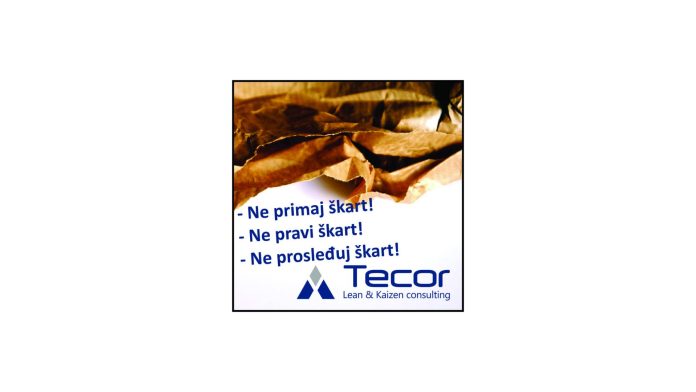
„Gde ima tu se i prosipa!“ Često možemo da čujemo ovu izreku u našem narodu. Najčešće na nekim veseljima gde se u zanosu prolije po koja čaša vina pa onda, da umanjimo nezgodu izgovorimo tu rečenicu praćenu osmehom i odobravanjem. No, dok par prosutih čaša i neki uflekani stoljnak možemo da u takvim trenucima ignorišemo, u proizvodnji, ukoliko imamo takva „prosipanja“ i „flekanja“ svaki dan, teško da ćemo to prihvatiti sa osmehom. Naprotiv, rasipanje materijala u proizvodnji nam je znak za uzbunu i poziv za njihovo eliminisanje. – poručuju iz domaće kompanije Tecor consulting.
Jedno od načela Lean filozofije je borba protiv takozvanih 8 smrtnih rasipanja (rasipanja materijala i vremena) a to su: defektni proizvodi (škart), prekomerna proizvodnja, prekomerna obrada, gomilanje zaliha materijala, nepotrebni transport, nepotrebni pokreti radnika, čekanja i nedovoljne veštine radnika. Što se tiče rasipanja materijalnih resursa moramo najpre da znamo koliki nam je ulaz materijala, odnosno utrošak, a kolika je realna količina proizvoda koju izbacujemo na tržište. Razlika je ono što negde „gubimo“ u proizvodnji, kroz rastur materijala ili defektne proizvode.
Zvuči jednostavno. Međutim, ono što moramo dalje da utvrdimo je gde nam se i kako ti gubici javljaju. Sprovođenjem Gemba šetnje – „idi vidi“ metode i stajanjem u krugu – posmatranjem procesa možemo utvrditi mesto i način javljanja rasipanja. Da li naše mašine proizvode defektne proizvode ili su defektni proizvodi rezultat nedovoljne obučenosti operatera, a možda nam je sam proces dizajniran tako da koristi više materijala nego što je potrebno. Upotrebom metode strukturnog rešavanja problema možemo da utvrdimo koren našeg problema, a samim tim i da sprovedemo akcije za njegovo uklanjanje. Ukoliko utvrdimo da naše mašine proizvode škart, da li su pravilno održavane? Sprovođenjem TPM-a – Totalnog produktivnog održavanja, kroz autonomno i plansko održavanje ali i fokusirano unapređenje opreme dovešćemo naše mašine u „fabričko“ stanje i smanjićemo mogućnost nastajanja defektih proizvoda. Ukoliko imamo neadekvatno obučene zaposlene, korišćenjem matrice veština možemo najpre da napravimo selekciju zaposlenih za pojedine poslove, a zatim da radimo na unapređenju njihovog znanja. Uvođenjem standarnih operativnih procedura olakšaćemo našim zaposlenima sticanje potrebnih znanja. Uređenjem radnog mesta na principima 5S metodologije, smanjićemo mogućnost da naš operater napravi grešku u proizvodnji jer će tačno znati gde mu se šta nalazi.
Samim redizajnom procesa možemo značajno smanjiti troškove rasipanja materijala. Da li naš proizvod pakujemo u neadekvatnu ambalažu, odnosno da li pakujemo i transportujemo vazduh? Optimizacijom ambalaže možemo da rešimo taj problem. Imamo li u našim procesima prekomernu obradu, odnosno da li se u našim procesima dešava neka aktivnost koja suštinski nije bitna krajnjem korisniku našeg proizvoda. Lean alatima kao što su statistička VA/NVA analiza i mapiranjem toka vrednosti možemo da najpre identifikujemo, a zatim uklonimo prekomerne procese obrade.
U većini procesa, ma koliko se trudili da ih optimizujemo neminovno će dolaziti do nastajanja otpada tokom obrade. Primera radi, obrada drveta, obrada metala ili izdvajanje koštica voća prilikom prerade. Sprovođenjem 5S metodologije i sortiranjem otpada, moći ćemo da ga recikliramo i da mu na taj način dodamo novu vrednost.
Još jedno pitanje može da se nametne prilikom utvrđivanja rasipanja, a to je koliko defekata možemo da tolerišemo? Škart od 1% možda ne deluje previše, recimo 10 komada na 1000 proizvedenih. Ali ukoliko proizvodimo milionske serije 1% je ogroman. Six Sigma metodologija može da nam odredi granicu prihvatljivosti i omogući uvid u naše gubitke. A ono što je jedan od ciljeva Lean filozofije, a to je potpuna elimanicija gubitaka uvek treba da nam bude vodilja i motiv za traženje poboljšanja.
Tekst priredio: Miloš Petrović, trener i konsultant, Tecor consulting